
It is a varied set to complement our polyurethane systems that allows the manufacture of products with different foams for every need.
They can be grouped into the two macro categories of rigid and flexible polyurethane systems.
Â
Rigid systems
With this polyurethane foam, moulded parts with a load-bearing structure are produced using RIM or RRIM technology, and it is possible to obtain moulded parts with a large surface area and low thickness at the same time.
These products have high mechanical performance and can replace various types of engineering plastics and thermosets in the automotive industry, a typical example being car and/or truck bumpers. The products are generally black or grey in colour and are normally produced with automated cycle plants. If produced using RRIM technology, they can be reinforced with glass fibre dispersed in the polymer. High- and low-pressure foaming machines are used for the production of manufactured goods.





Polyurethane foam called structural foam is used for the production of products with a load-bearing structure.
The result is products that combine high mechanical properties with very low weights. These characteristics are achieved by the progressive increase in the density of the artefact, a density that increases from the centre outwards. The production cycle involves the use of moulds with temperatures between 45 and 65°C, preferably made of metal. RIM technology is used to obtain extremely dimensionally accurate artefacts. This polyurethane foam is also widely used ‘by casting’.
High or low pressure foaming machines are used for the production of manufactured goods.



Low-density rigid systems foamed with water or water/HFC (depending on the intended use of the product) are foams with a final density generally between 40 and 80 g/l, mainly used as thermal insulation or light fill.
In order to meet the restrictions imposed by fire behaviour regulations, the formulas can be supplemented with flame retardants. The application field of these systems is hot/cold insulation generally with operating surface temperatures not exceeding 80°C.
Some examples of use: refrigeration bodies for industrial applications, air conditioning, home and industrial refrigerators, refrigeration equipment, sandwich panels, insulation of boilers and tanks, insulating back foams, filling castings of various volumes, insulation with spray application, filling of profiles with continuous casting.
We can also include the production of various and complex shapes for theatre/cinema, for furniture, for tailoring and the production of moulds/preforms for various technical applications.
High- or low-pressure foaming machines are used to produce items with this system.






This is a specific application possibility that takes its cue from its counterpart technology applied to thermoplastics.
Thanks to a special viscosity profile of the system, several millimetres of polyurethane can be distributed on the inner surface of a mould. The 2-axis mould production and handling system allows the internal surface of the mould to be wetted and the thickness to be created without the entire mass falling back on itself. The processing cycles obtained are between 10 and 14 minutes depending on the shape required.
High- or low-pressure foaming machines can be used.

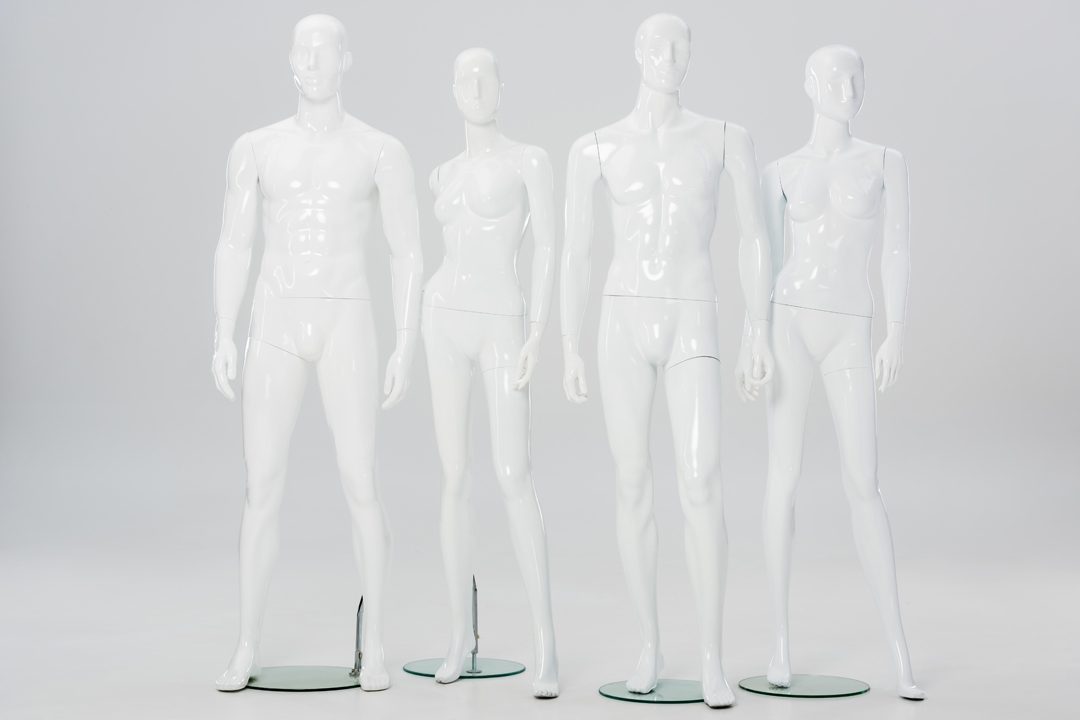
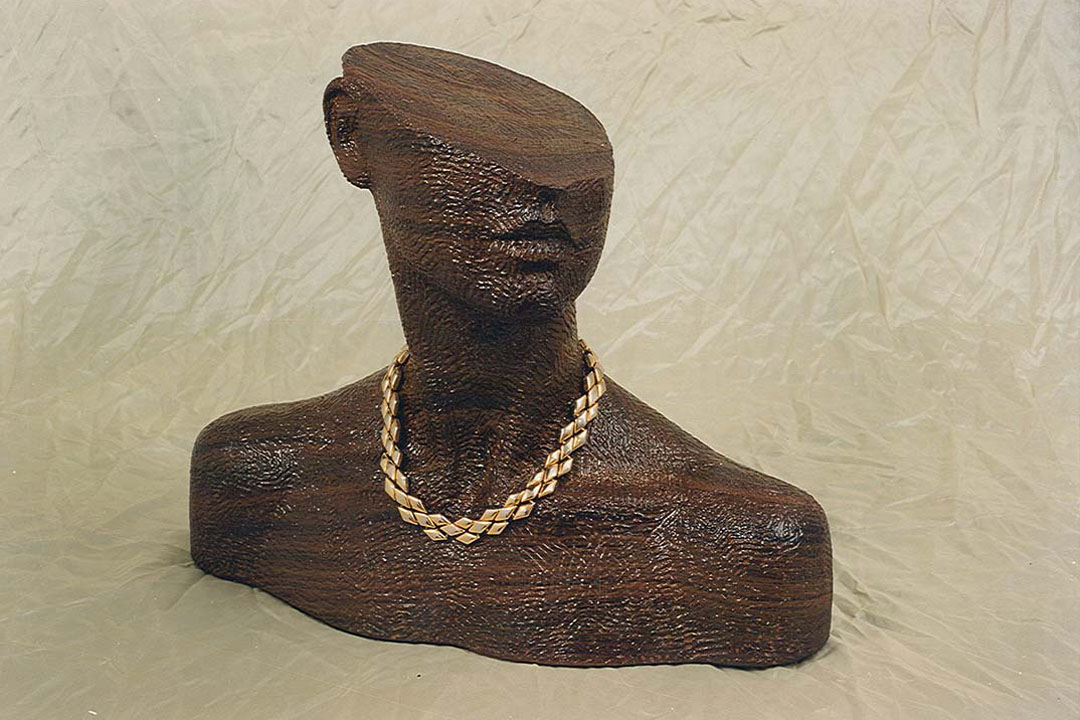
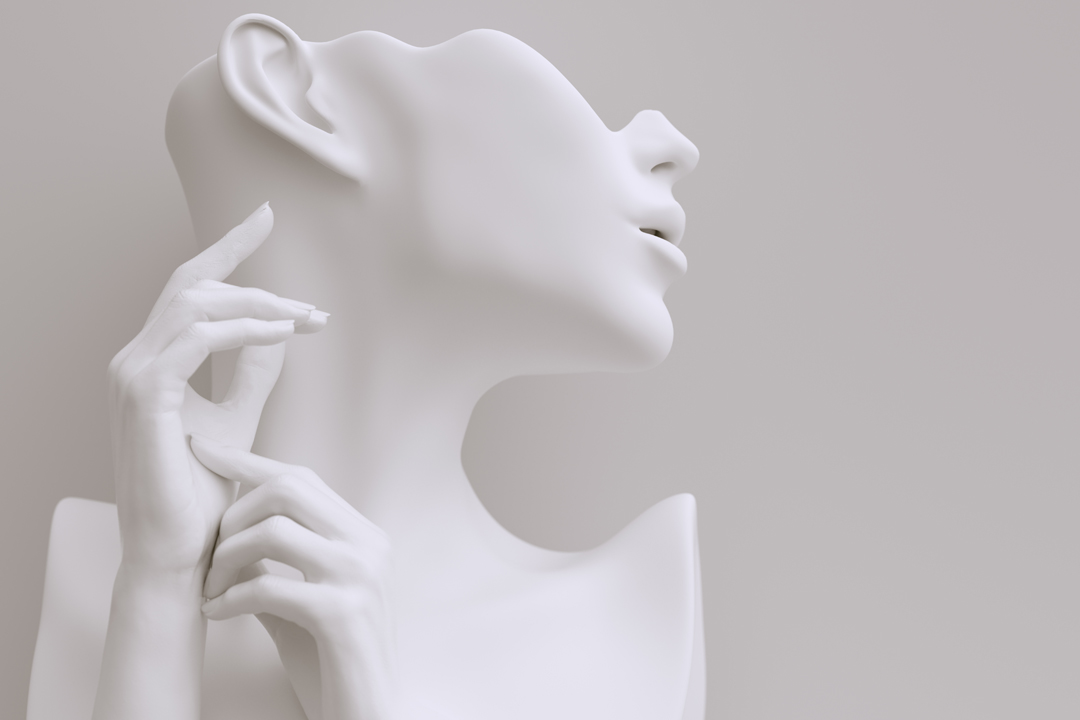

Aropack is a versatile foam for use in the packaging industry and enables the production of perfect packaging regardless of the shape, size and weight of the objects to be packed.
The main advantages of Aropack foam are:
- Ease of use – The Aropack system involves the use of a dispenser, equipped with a self-cleaning cartridge connected to the dispensing pumps of the two components, which together with an automatic diagnostic system ensures constant quality and continuous computerised control
- Reduction of Warehouse Space – Aropack foam has the special feature of expanding up to 150 times, with two drums of raw material you can produce foam for the volume of a lorry
- Adaptability to Shapes – With Aropack foam, there are no limits to the shapes, weights and sizes of the objects to be packed because the extreme adaptability of the foam allows any type of object to be packed
- Maximum Protection – Aropack foam is formulated to allow maximum protection of objects during all phases of handling and delivery
- Speed – With Aropack foam, in just one step, items are packed and placed in the shipping box. The ease of use and characteristic reactivity of the resin allow for fast packing in any condition and for any object
- Economy – The advantages indicated so far lead to a simple conclusion: Aropack foam is certainly convenient and economical. The low installation cost and the reduction of packaging time and storage space offer all the economic advantages that a company seeks on a daily basis
- Recyclability – The possibility of reusing packaging for other shipments, the cleanliness of the wrapping and the complete eco-friendliness of Aropack foam are the winning factors for the new packaging frontier

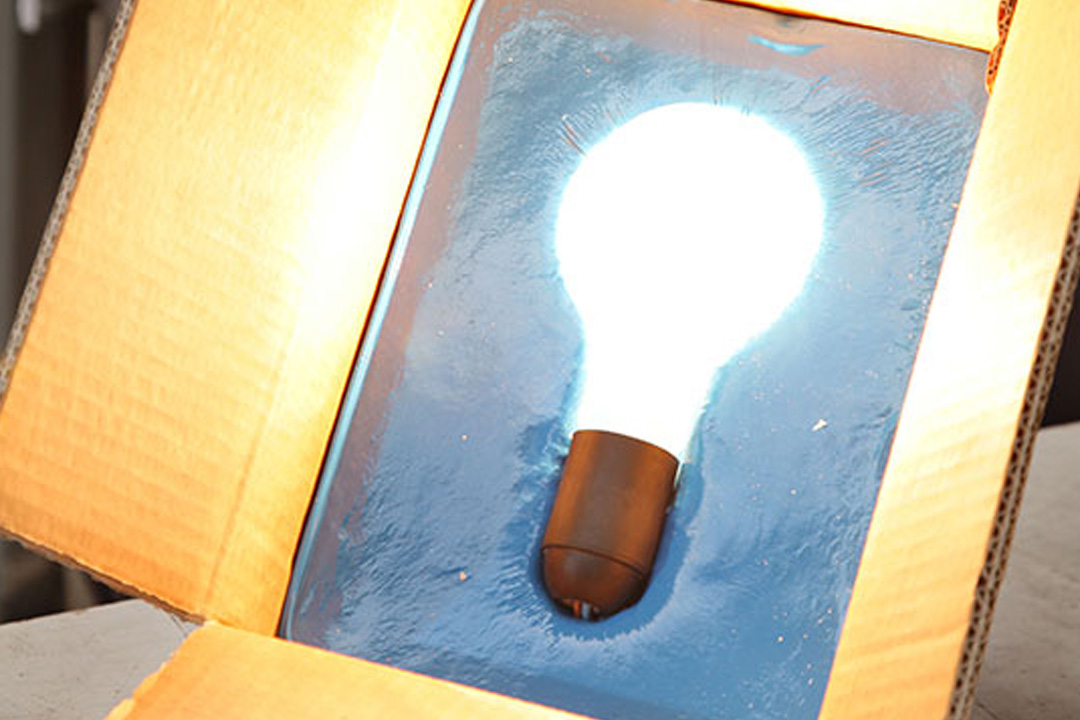

Low-density rigid polyurethane spray is preferred to traditional insulation methods because it offers:
- insulation without thermal bridges even in the case of complex shapes and/or very large surfaces
- adhesion of the foam to the surface to be insulated, including ceilings and vertical walls
- speed of execution.
PU SPRAY is applied in much the same way as a varnish and the manual skill required is the same, the only difference being that the thickness contained in a few millimetres of applied PU expands and solidifies within seconds.
The density and insulating properties are obviously the same as those of polyurethane for thermal insulation. Reacting directly on the surface to be insulated, the material clings to the substrate, forming a monolithic coating on both flat and complex surfaces, regardless of position or inclination.
Surfaces of thousands of square metres, as in the case of industrial sheds, can be insulated from heat and cold seamlessly and thus without thermal bridges, in a very short time. Subsequent alterations to structures can be done without difficulty and re-insulated by spraying PU on top of the pre-existing one.
Although designed for the building industry, these systems are also used in petrochemical plants or tankers, for the insulation of large tanks with rounded shapes, and can be done directly on site, thus eliminating the difficulties and high costs of handling.
High- or low-pressure foaming machines are used to produce items with this system.

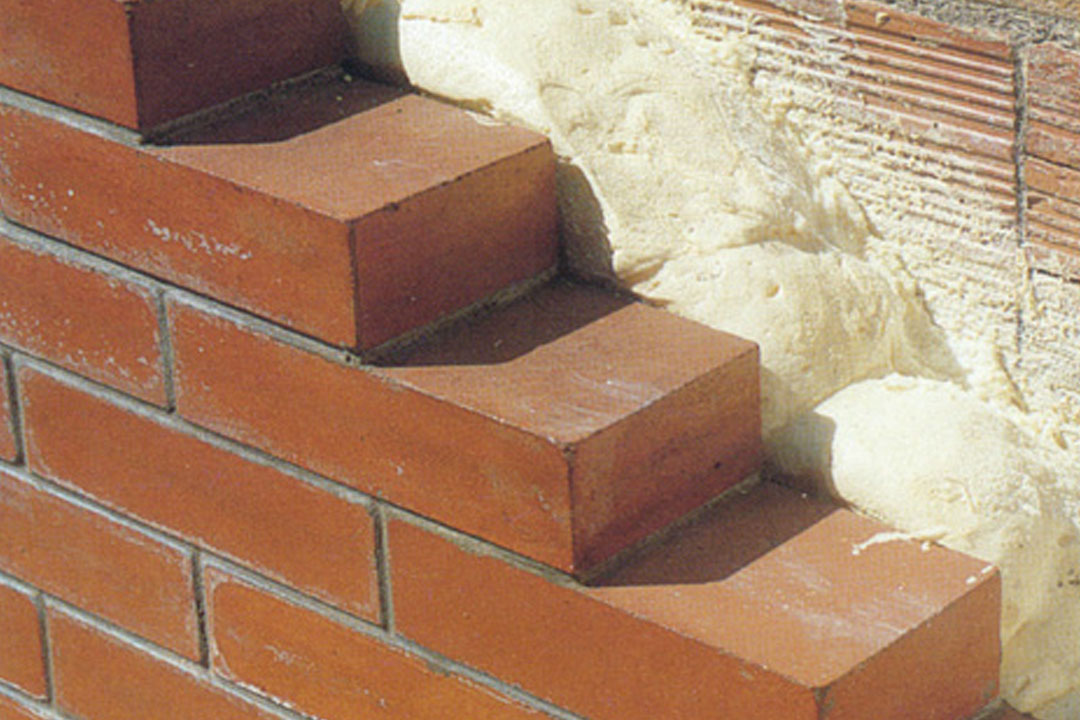
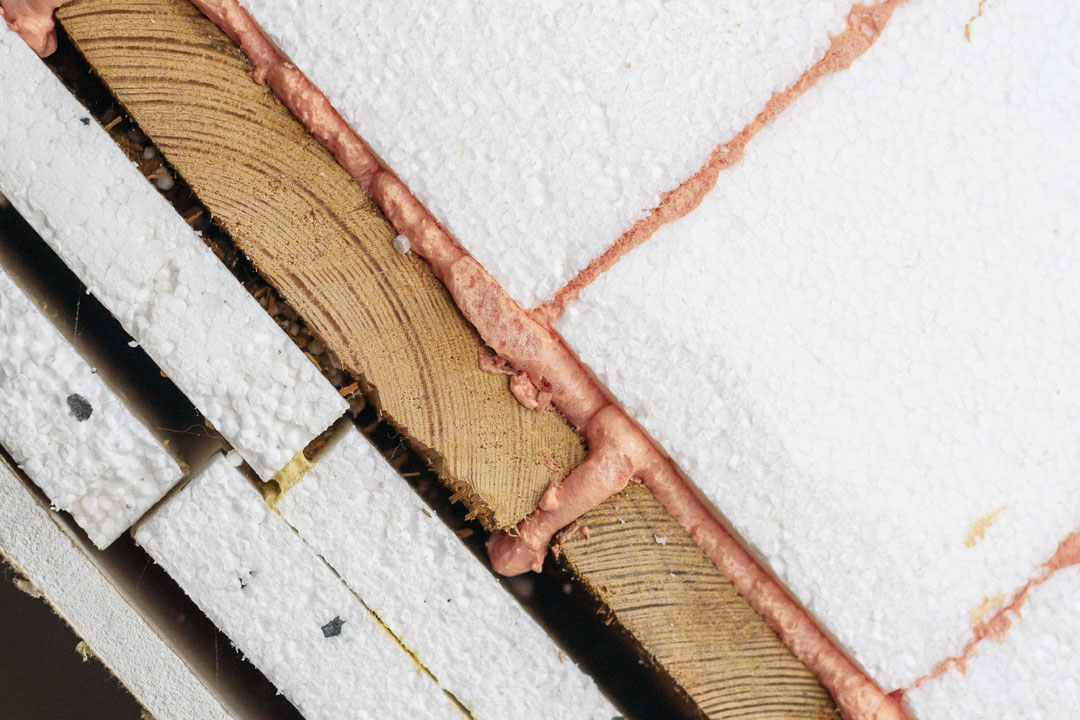
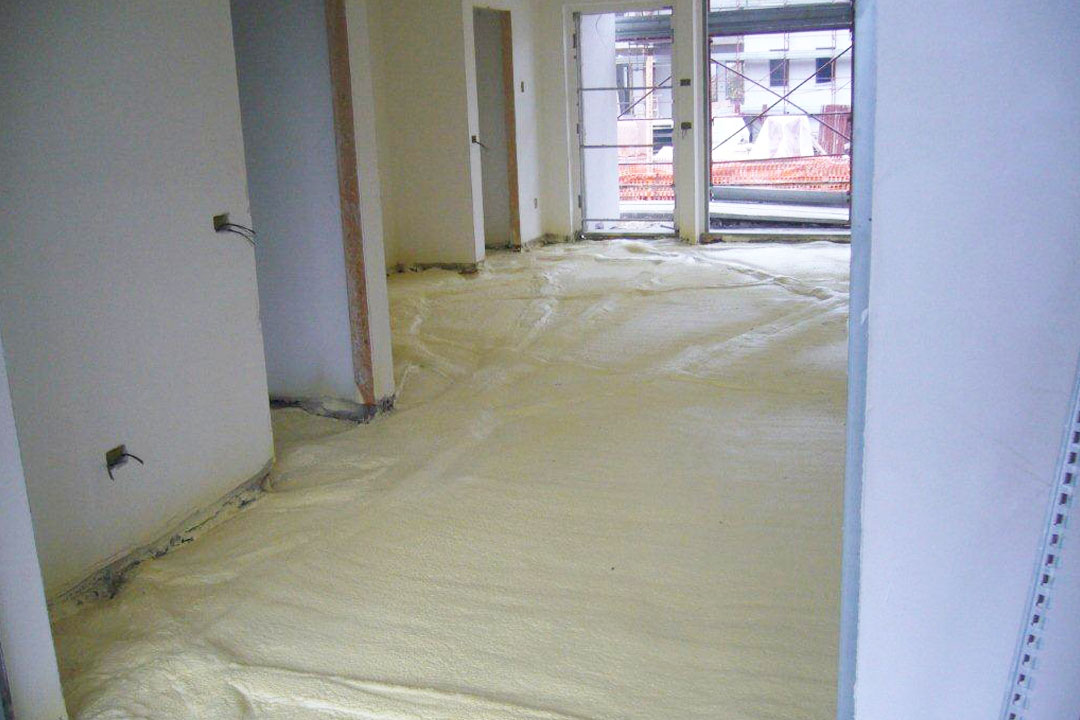


Flexible systems
This polyurethane system is used for specific applications such as mattresses and pillows, with which it is possible to produce moulded parts with densities between 50/80 grams/litre.
The AROFLEX SMB system offers very little resistance to crushing, as it slowly recovers its original shape once compressed. The moulded product is normally neutral in colour.
Both high-pressure and low-pressure foaming machines are used for the use of this polyurethane foam.





Semi-rigid foams find application in very different sectors. These are products that combine a rigid consistency at rest with an elastic response when subjected to impact. In addition to this performance, the moulded part is lightweight, with densities generally between 80 and 160 g/l.
These foams are used to produce moulded parts capable of absorbing high energies (impact resistance) with rather little deformation. These polyurethane foams are used in the moulding of bumpers, possibly in combination/reinforcement with the polypropylene moulded part. The sports sector offers multiple application opportunities due to the lightweight of the moulded parts, especially when the formula requires high strength against compression but not elongation. This system is commonly used for the production of helmets, reinforcements for sportswear (shoulders, knees and back), targets and animal shapes for archery.
Both high-pressure and low-pressure foaming machines are used for production.



The market has a fairly frequent need for rubber products with hardnesses between 40 and 80 Shore A, for applications where the essential mechanical performance does not require extreme operating temperatures.
Small production amounts impose simple production methods with very low investment in moulds and moulding and are certainly incompatible with the investment in metal moulds and injection moulding machines required for the use of sophisticated technopolymers.
Examples of such applications are the coating of rollers, road speed bumps, buffers, various items for industrial use, inserts for safety clothing, handles and knobs, and furniture applications. When used for visible parts, these products are generally pigmented black, but for special aesthetic requirements, the customer can independently pigment and/or paint the parts with the products that best meet their needs. Both high-pressure and low-pressure foaming machines are used for production.




